Digital Workflow
We define the digital workflow as any work protocol that is carried out using digital methods from diagnosis to the completion of treatment. The digital workflow is divided into a sequence of phases: Digitization, Design, and Production.
Contactar02
Fase
Design
Once we have received the STL file in the laboratory, the Design phase or CAD phase begins.
More information03
Fase
Production
Once the prosthesis is designed, it moves to the final Production phase or CAM phase.
More information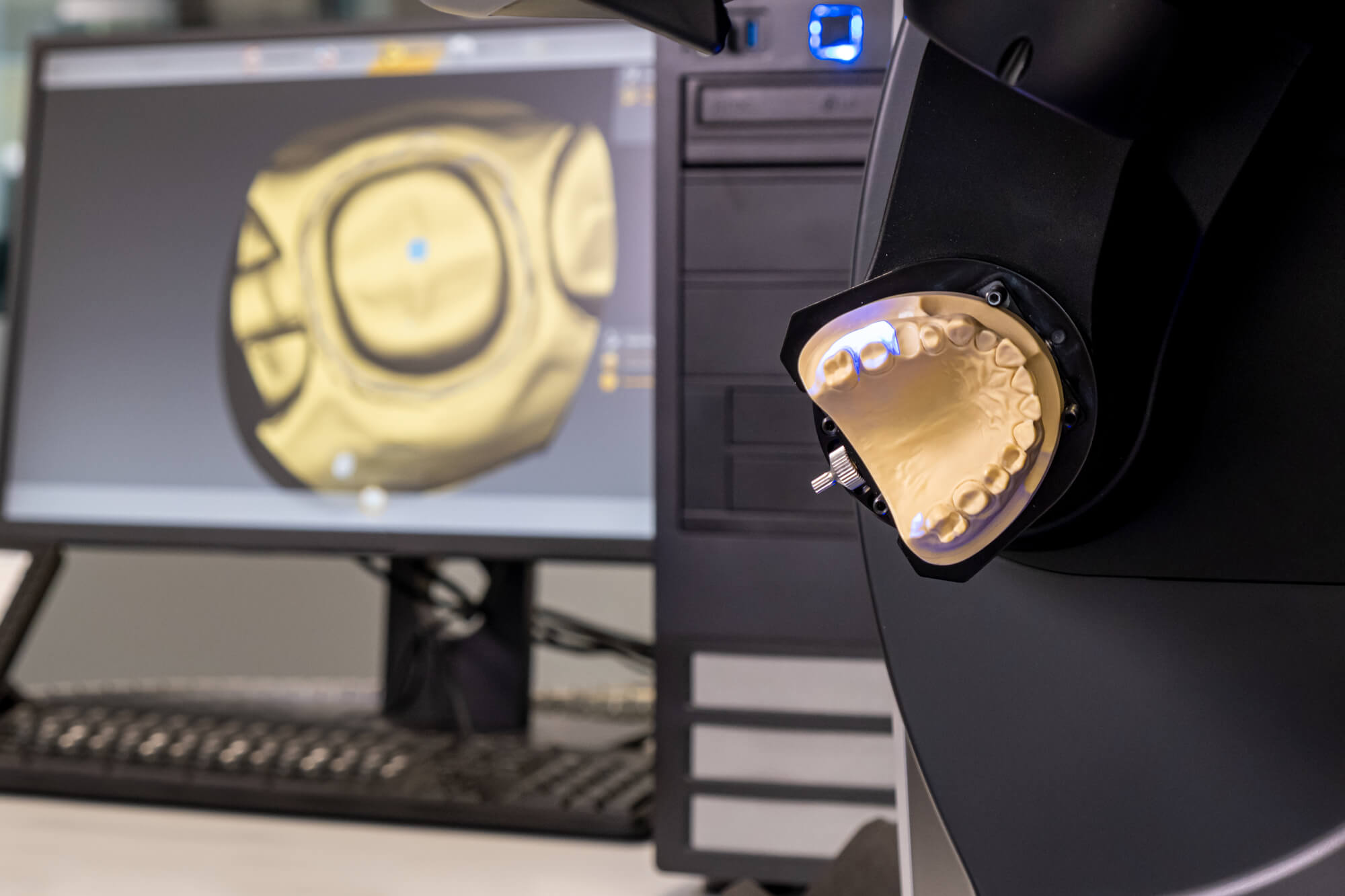
01
Digitization
In the first phase of digitization, scanners play a key role. In the laboratory, we have all three types of scanners available:
Extraoral Scanner
These scanners allow us to transform analogical work (traditional) such as silicone or alginate impressions into a 3D file that can be opened in design software (CAD).
Intraoral Scanner
Typically used in the clinic, intraoral scanners capture precise images directly from the patient's mouth. This scan creates a digital file (STL) that is sent directly to the laboratory, allowing us to receive all the necessary information into our design software.
Facial Scanner
This scanner captures the patient's face and translates it into 3D data.
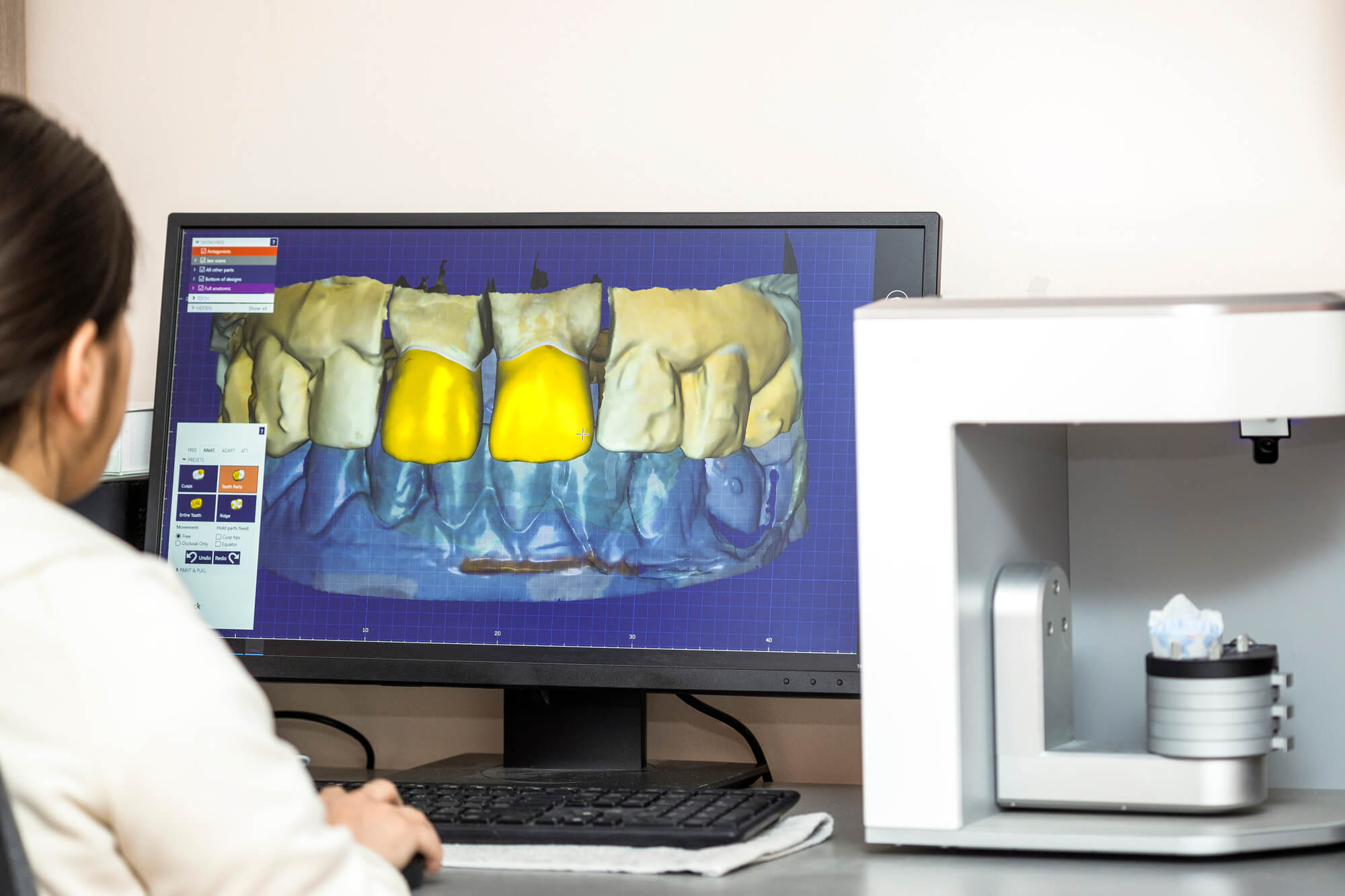
02
Design
Once we have received the STL file in the laboratory, the Design phase or CAD phase begins.
In this phase, our technical designers open the case in the design software. Ceranium works with Exocad CAD Design. This software allows us to design the work based on the specific needs or requirements of the doctor.
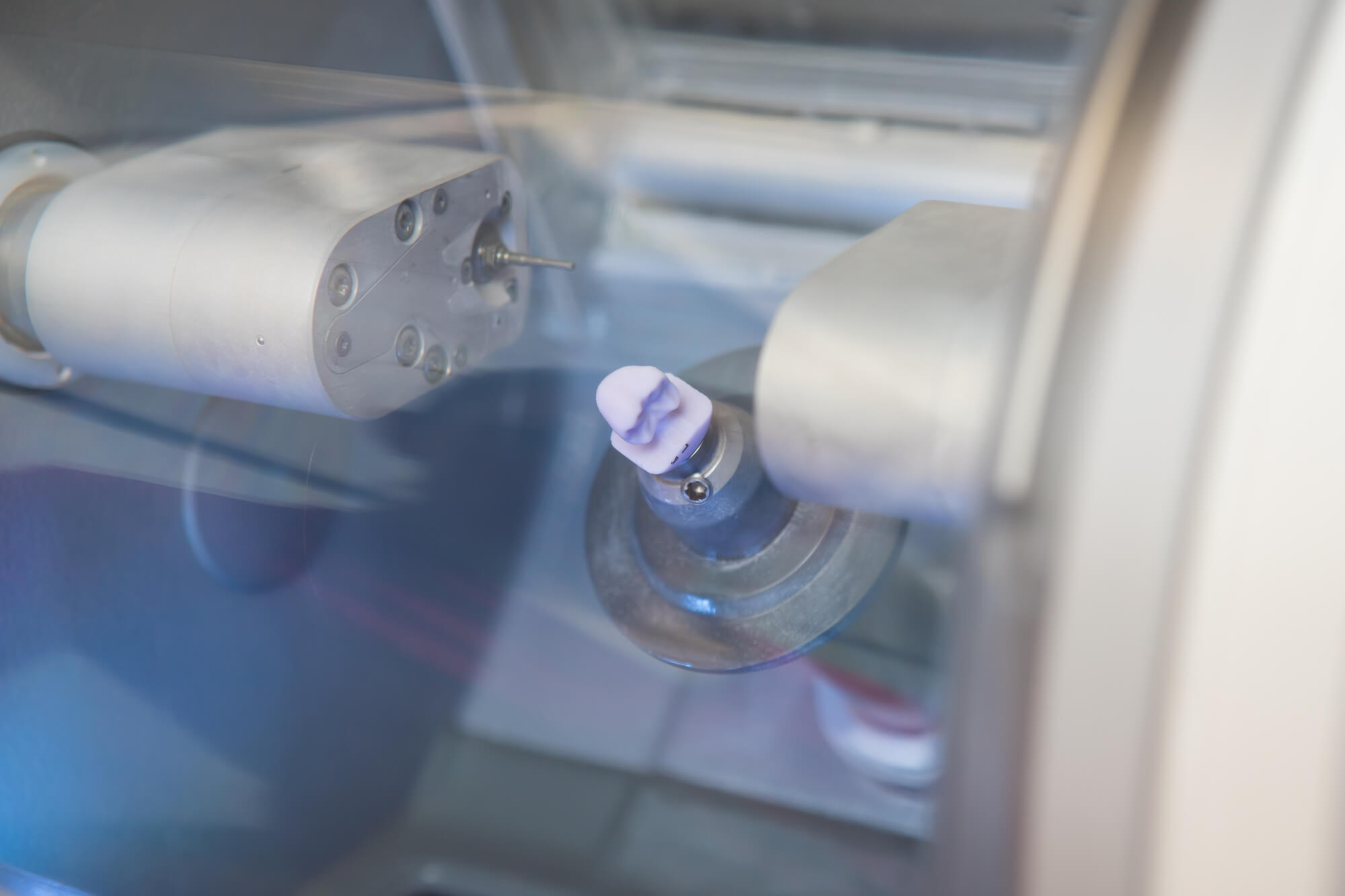
03
Production
Once the prosthesis is designed, it moves to the final Production phase or CAM phase.
In this phase, the most common manufacturing practices in a laboratory are:
Machining
This technique involves gradually removing layers of material. We perform this process through milling. In the laboratory, we work with two types of mills—wet and dry milling. This technology allows us to work with more durable and higher-quality materials, such as Zirconia and Lithium Disilicate.
Post-machining
In this technique, the structure is sintered, and the connection with the implant is milled. In our laboratory, this technique is outsourced.